What is thermoforming: process, materials & more - full guide
- Posted on
- Posted in Arts & Crafts, Food, Home decor

Thermoforming is a versatile and cost-effective manufacturing process to shape plastic sheets. In this comprehensive guide, we'll explore what thermoforming is, how it works, its processes, its applications, and its benefits. Let’s start!
Thermoforming is a versatile and cost-effective process used to shape plastic sheets. In this detailed guide, we'll explore what thermoforming is, how it works, its various processes, applications, and benefits. Let’s begin!
What is thermoforming?
Thermoforming is a dynamic plastic manufacturing process that uses heat, combined with pressure or vacuum, to transform flat plastic sheets into intricate 3D shapes. This method is not only easy to execute but also cost-effective.
The basic principle of thermoforming involves heating a thermoplastic sheet until it becomes pliable. Once softened, the sheet is placed over a mould or die, where it is shaped by applying vacuum pressure or mechanical force. This process allows for the creation of highly detailed and precise shapes. Modern thermoforming machines often include trimming and cutting functions, which streamline the production process.
Thermoforming enables manufacturers to produce high-quality plastic parts of all sizes with precision and efficiency, catering to the demands of various industries and end-users. Its ability to create complex shapes with ease and affordability makes it a valuable asset in modern manufacturing processes.
The thermoforming process
Thermoforming typically involves several key steps: sheet heating, moulding, cooling, and trimming.
Sheet heating
The process begins with heating a flat plastic sheet, usually made of materials like PVC, PET, or ABS, until it becomes pliable. This is done using radiant heaters, infrared heaters, or convection ovens.
Moulding
Once heated, the plastic sheet is transferred to a mould, usually made of metal, and shaped using vacuum pressure or mechanical force. Depending on the application, different moulding techniques may be used, such as vacuum forming, pressure forming, or twin-sheet forming. Let’s explore more details about these techniques:
-
Vacuum forming
The plastic sheet is heated and draped over a mould, and a vacuum is applied to draw the material tightly against the mould’s contours. This process ensures a precise replication of the mould's shape on the plastic surface. The vacuum is generated underneath the sheet, gradually pulling it against the mould cavity until it conforms to the desired shape. Building prototypes via vacuum forming is relatively straightforward compared to other thermoforming methods, making it a popular choice for various applications. -
Pressure forming
Additional pressure is used alongside vacuum to create shapes with finer details and sharper edges. This makes pressure forming ideal for products requiring complex detailing. -
Twin sheet forming
Two plastic sheets are heated and shaped simultaneously, then fused together around the edges. The formed sheets are then joined together around the mould perimeter and air pressure is typically injected between the sheets to facilitate bonding. Twin sheet forming excels in creating hollow plastic parts or components with double walls. -
Mechanical forming
Mechanical force is applied, often using a press, to shape the plastic against the mould. This method is commonly employed for producing parts with intricate details or deep draws, ensuring precision and high levels of detail in the final product. -
Drape forming
A heated sheet is draped over a mould, allowing gravity and simple tooling to shape the plastic. The simplicity of the method contributes to its affordability, making it an attractive option for manufacturers seeking cost-effective solutions for shaping plastic materials. -
Matched mould forming
Involves two moulds (a male and a female) that shape the heated sheet, providing tight seals and dimensional control. This makes it ideal for creating intricate shapes or patterns with precision. Matched mould forming has applications in industries requiring high accuracy, such as automotive and medical device manufacturing. -
Billow forming
Used for creating hollow or rounded shapes, where air pressure blows the heated plastic into a mould cavity.
Each of these thermoforming techniques has its own advantages, depending on the complexity of the part, material properties, and production needs.
Cooling and trimming
After moulding, the plastic is rapidly cooled using air or water to solidify its shape. Excess material is then trimmed away to produce the final product. Modern machines often integrate these trimming processes, reducing waste and improving efficiency.
Thermoforming materials
Several plastic materials are commonly used in thermoforming, each chosen for its specific properties:
PVC (Polyvinyl Chloride)
Known for its strength, chemical resistance, and durability, PVC is used in applications ranging from construction to automotive interiors.
It is a common material for vacuum forming, and our FORMART all-in-one vacuum formers handle PVC very well.
PET (Polyethylene Terephthalate) and PETG (Polyethylene Terephthalate Glycol)
Valued for its clarity and toughness, PET(G) is commonly used in packaging, especially for food and beverages. Additionally, PET(G) is highly recyclable and transparent to microwave radiation, though post-forming drying is required to enhance its resistance.
Widely utilised in bottles, synthetic fibres, and specific food products, PET(G) remains a versatile and indispensable material in various industries.
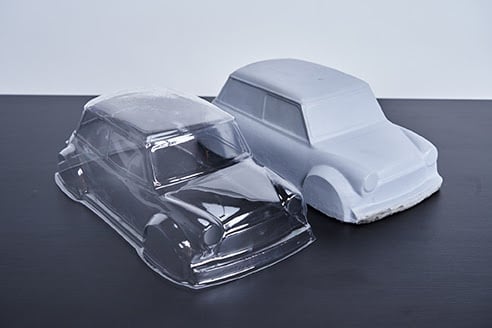
ABS (Acrylonitrile Butadiene Styrene)
ABS offers a strong blend of impact resistance and heat resistance. From sports equipment, food containers, and automobile parts to electronic devices and piping systems, ABS is a versatile material choice.
PP (Polypropylene)
Versatile and affordable, PP is used in a wide range of products, including packaging and medical devices.
HIPS (High Impact Polystyrene)
HIPS is a tough, cost-effective material often used in food containers, packaging, and retail displays.
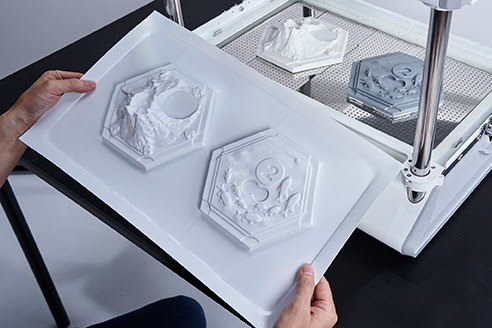
PC (Polycarbonate)
Known for its strength and clarity, PC is used in products requiring durability, such as eyewear lenses, medical devices, automotive parts, protective gear, bullet-proof glass, safety glass, and construction materials.
HDPE (High-Density Polyethylene)
With excellent moisture and chemical resistance, HDPE is ideal for packaging and industrial applications.
Other materials
EVA (Ethylene Vinyl Acetate) is typically not suitable for vacuum forming.
However, if it is less than 2.5 mm thick, EVA can be formed with FORMART vacuum formers, albeit with limited detail reproduction.
PVDF (Polyvinylidene Fluoride) is commonly used in injection moulding, but it is not suited for vacuum forming due to its low glass transition temperature (Tg).
Heavy vs. thin gauge thermoforming
Thermoforming is categorised into heavy gauge and thin gauge processes, based on the thickness of the plastic sheets used. Heavy gauge thermoforming handles thicker sheets (1.5 to 9.5 mm), while thin gauge thermoforming works with thinner sheets (less than 3 mm), typically fed from rolls.
Aspect | Heavy gauge thermoforming | Thin gauge thermoforming |
---|---|---|
Sheet thickness | 1.5 - 9.5 mm | Less than 3 mm |
Material source | Sheets | Rolls |
Thermoplastic materials | ABS, PP | PET, PVC |
Equipment | Cut-sheet thermoforming machines | Roll-fed thermoforming machines |
Ideal applications | Large parts, heavy-duty items, like car parts | Small parts, high-volume production, like food packaging |
Production speed | Slower | Faster |
Production volume | Low to medium | Medium to high |
Each of these processes and materials offers unique advantages, making thermoforming a valuable technique in modern manufacturing across various industries.
Thermoforming equipment
A thermoforming machine shapes plastic sheets over objects by heating the material and vacuuming air, used across industries for diverse applications. However, thermoforming equipment isn't a one-size-fits-all solution. Learning how to choose the perfect type of machine for your needs is the key. Let’s explore industrial, desktop, and DIY options:
Industrial thermoforming
Ideal for high-volume production and complex components, industrial thermoforming machines are equipped with large forming areas to accommodate sizeable and intricate parts. They feature deep draw capabilities, allowing for a wide range of plastic sheet thicknesses, and powerful vacuum forces suitable for various materials. These machines are highly automated for efficiency, with rapid tool-changing mechanisms. However, they come at a higher cost due to their advanced features and industrial-grade construction.
Desktop thermoforming
Desktop thermoforming machines are well-suited for small-scale production, prototyping, or hobbyists. These compact machines offer basic functionalities and smaller forming areas, yet they remain versatile enough to produce a variety of parts. Although they provide limited draw depth and lower forming force, they allow for manual or semi-automated operation, giving users greater control. Compared to industrial machines, they are a more affordable entry point.
DIY thermoforming
DIY thermoforming is a budget-friendly option for beginners, utilising household tools and materials for basic experimentation. This approach has a very limited forming area and depth, relying heavily on manual manipulation and improvisation. While it is not suitable for professional applications or high-quality production, it offers an economical way to explore thermoforming techniques.
Industrial | Desktop | DIY | |
---|---|---|---|
Production volume |
High |
Small | Very small |
Forming area |
Large | Small |
Extremely small |
Automation | High | Manual / semi |
Manual |
Cost | Expensive | Affordable |
Very affordable |
Unlock limitless design possibilities and accelerate your prototyping with MY YARD’s desktop vacuum forming solutions. Start your project today!
How to choose thermoforming moulds
Choosing the appropriate moulds for thermoforming requires careful consideration of various factors to ensure optimal performance and efficiency.
Firstly, evaluate the production volume to determine the most cost-effective mould material. For custom parts or prototypes, which typically involve low volumes, materials such as wood, plaster, composites, or 3D-printed plastics are suitable. In contrast, high-volume production benefits from metal moulds due to their superior durability and thermal conductivity.
Secondly, assess the complexity of the part design, opting for precision machining or 3D printing for intricate geometries.
Lastly, consider the thermoforming temperature requirements and the forces involved, ensuring the mould can withstand specific material types and thicknesses while optimising part quality and the demoulding process.
Remember: the key to a successful mould lies in understanding your project’s requirements. Analyse the complexity of the part, production volume, and thermoforming conditions (temperature, pressure) to select the most suitable material and fabrication method.
Benefits of thermoforming
Thermoforming offers several advantages over other manufacturing processes, including:
Cost-effectiveness
Compared to injection moulding or machining, thermoforming is particularly economical for large-scale production. Its lower tooling costs and efficient production processes contribute to significant cost savings.
Lightweight and durable final products
Thermoforming produces lightweight yet remarkably durable products, offering exceptional strength and resilience against impacts. This durability stems from the unique properties of thermoplastic materials used during thermoforming. These materials not only ensure longevity but also guarantee enduring performance, making them ideal for a wide range of applications.
Fast turnaround times
Thermoforming offers quick production cycles, ensuring rapid turnaround for finished products. Its efficient process and streamlined workflows enable manufacturers to meet tight deadlines and respond swiftly to market demands. Additionally, thermoforming facilitates rapid and cost-effective prototyping, enhancing product development efficiency and reducing time-to-market.
Design flexibility
Thermoforming offers unmatched design freedom, allowing for the creation of intricate shapes, textures, and surface finishes. This flexibility empowers designers to unleash their creativity, resulting in innovative and visually striking products that stand out in the market.
Applications of thermoforming
Thermoforming is widely used across various industries. Common applications include:
Packaging
Thermoformed trays, clamshells, bottles, jars, and blister packs are extensively used for packaging a variety of products, including food, electronics, cosmetics, and medical devices.
Mould replication
Thermoforming is commonly used in industries such as chocolate moulding or resin casting, where replication involves creating duplicates of solid objects using thermoformed moulds. This technique, often associated with desktop vacuum forming, enables precise replication of shapes and details for various applications.
Automotive
Thermoformed parts are used in automotive interiors, including dashboards, door panels, and trim pieces.
Consumer goods
Thermoforming is prevalent in the production of consumer and household goods, ranging from disposable cups and trays to cosmetic packaging.
Signage and displays
Thermoforming is used to create aesthetic signage, displays, and promotional materials due to its ability to be formed into various shapes and incorporate branding elements with different textures.
Aircraft interiors
Thermoformed plastics are used in aircraft cabins for components such as window panels, seat armrests, and overhead bins.
Medical devices
Thermoformed trays and housings are crucial for medical device packaging, ensuring sterility and protection during transportation. Thermoforming also contributes to the production of prosthetics and orthotics, providing custom-fit solutions for patients' needs.
MY YARD offers the best desktop vacuum forming solution for thermoforming
Thermoforming is a versatile and cost-effective manufacturing process with numerous applications across various industries. Whether for packaging, automotive components, or consumer goods, thermoforming offers unparalleled design flexibility, cost-effectiveness, and rapid prototyping capabilities.
Embrace the potential of thermoforming in modern manufacturing with MY YARD. From packaging to mould replication, our desktop vacuum forming machines provide rapid prototyping capabilities with exceptional design flexibility.